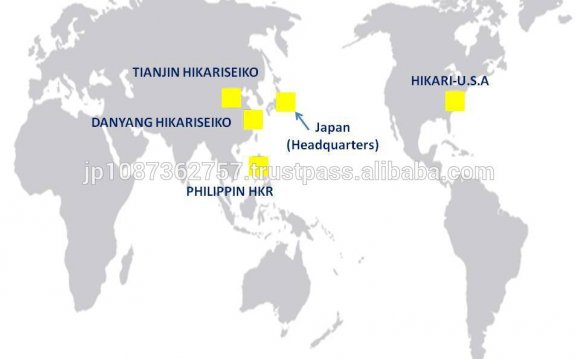
This application is a continuation-in-part of copending U.S. patent applications Ser. Nos. 121, 081, filed Feb. 13, 1980 and 147, 672, filed May 7, 1980, now U.S. Pat. No. 4, 314, 852.
DESCRIPTION1. Technical Field
The field of art to which this invention pertains is internal combustion engines, and specifically combustion chamber components.
2. Background Art
In an attempt to make motorized vehicles more energy efficient, recent attention has turned to the use of nonmetal composite materials. For example, as described by V. A. Chase ("Automotive Applications of Composite Materials" published on pages 388-398 in the Proceedings of the 11th National SAMPE Technical Conference, Nov. 13-15, 1979, Boston, Mass.), General Motors has been using fiber reinforced plastics in their automobiles as body components since 1953, but few other applications have received attention until recently. Automotive areas where these fiber reinforced plastics have begun to receive attention are in such things as leaf-springs, coil-springs, stabilizer bars, and even such things as drive shafts. And while non-metallic composites have been considered for use in internal engine components, because of the high temperature instability of such components, their use has generally been limited to the lower temperature components of the internal engine environment. For example, Chase documents the fact that attempts at using a fiberglass-epoxy composite piston in an internal engine environment resulted in gradual degradation of the piston surface due to the thermal effects produced in the engine.
Similarly, Kamo et al ("Ceramics for Adiabatic Diesel Engine", Proceedings of the Workshop on High-Temperature Materials for Advanced Military Engines, Vol. II, pages 367-390, Institute of Defense Analysis, Washington, D.C., Paper No. P-1421, published September 1979) discloses that while ceramics have many desirable properties which would suggest their use as metal replacements in the internal combustion engine environment, such things as their low material strength and distortion under heating has made their use impractical. Accordingly, what is needed in the art are non-metallic internal combustion engine components with high strength, high fracture toughness, and oxidation stability at high temperatures.
DISCLOSURE OF INVENTIONThe present invention is directed to a solution to the use of non-metallic composites in an internal combustion engine, which composites can withstand the high temperatures produced in such engine and still maintain their high strength and oxidative stability. The solution to this problem is the use of fracture tough silicon carbide fiber reinforced ceramic or silicon carbide fiber reinforced glass with high temperature strength, high temperature oxidation stability, and good heat insulating properties as internal combustion engine combustion chamber components.
One aspect of the invention includes the use of components comprising a multilayered-fiber reinforced ceramic made up of a plurality of ceramic layers, each layer reinforced with a plurality of unidirectional, continuous length silicon carbide fibers, each layer having an axial flexural strength greater than 70, 000 psi and a high fracture toughness, exemplified by a critical stress intensity factor greater than 10×103 psi (inch)1/2.
Another aspect of the invention includes the use of components comprising silicon carbide fiber reinforced borosilicate glass with flexural strengths above about 60, 000 psi maintainable at temperatures up to about 600° C.
Another aspect of the invention includes the use of components comprising silicon carbide fiber reinforced high silica content glass with flexural strengths above about 60, 000 psi maintainable at temperatures up to about 1150° C.
Another aspect of the invention includes the use of components comprising silicon carbide fiber reinforced aluminosilicate glass with flexural strengths above about 75, 000 psi maintainable at temperatures up to about 700° C.
Another aspect of the invention includes an internal combustion engine containing combustion chamber components made of the above recited composite materials.
The foregoing, and other features and advantages of the present invention, will become more apparent in light of the following description and accompanying drawing.
BRIEF DESCRIPTION OF THE DRAWINGSFIG. 1 shows in cross section an actual uniaxial silicon carbide fiber reinforced ceramic matrix composite component according to the present invention.
FIG. 2 shows in cross section an actual multiaxial silicon carbide fiber reinforced ceramic matrix composite component according to the present invention.
FIG. 3A shows graphically flexural strength data for a borosilicate glass composite component reinforced with silicon carbide yarn according to the present invention.
FIG. 3B shows graphically flexural strength data for a borosilicate glass composite component reinforced with large diameter silicon carbide monofilaments according to the present invention.
FIG. 4 shows graphically flexural strength data for a high silica content glass composite component according to the present invention.
FIG. 5 shows flexural strength data for an aluminosilicate glass composite component according to the present invention.
FIG. 6 shows in cross section an internal combustion engine combustion chamber with components according to the present invention.
FIG. 7 shows a cylinder head hot plate component according to the present invention.
BEST MODE FOR CARRYING OUT THE INVENTIONRELATED VIDEO
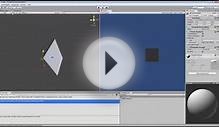
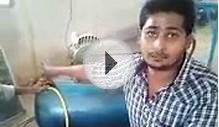
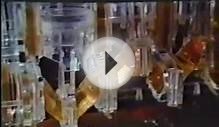