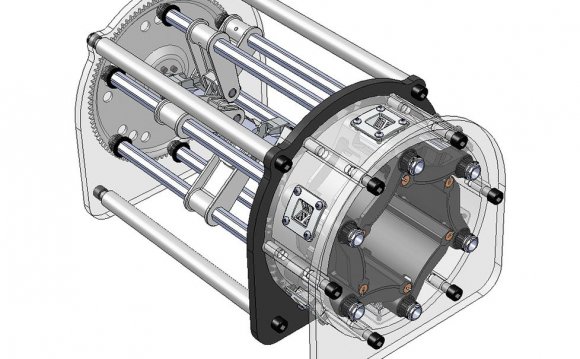
Each of the alternative engine architectures discussed here have one major feature in common with the standard piston engines that have dominated the automobile for more than a century: Fuel is burned inside a chamber to convert chemical energy into mechanical energy for propulsion. However, that requires moving air and fuel in and exhaust gases out of the combustion chamber, all of which adds complexity and reduces efficiency.
In 1816, Scottish inventor Robert Stirling conceived of the closed-cycle engine with the working fluid (in this case, air) remaining contained within the device. The heat source—which could be almost anything, including combustion—is external to the engine. Like the Ecomotors OPOC and the Scuderi, pairs of pistons operate together to provide the complete cycle. The air in one chamber is heated via heat transfer through the cylinder wall pushing back the displacer piston, which is linked to a second power piston in the expansion chamber. As the heated air continues to expand, it displaces the power piston, which drives a crankshaft that produces rotational torque. As the air cools, both pistons move back to their original positions, and the process repeats.
Until recently, Stirling engines were mainly used for stationary applications—in part because they were not suitable for typical transient applications where the power delivery varied significantly over time. However, newer configurations and the ability to use alternative fuels have revived interest, especially for range-extender applications where constant speed operation and low noise (due to the continuous external combustion) are beneficial.
RELATED VIDEO
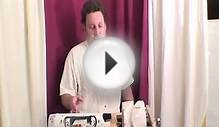
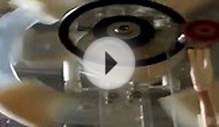
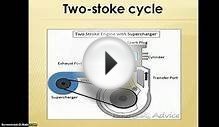