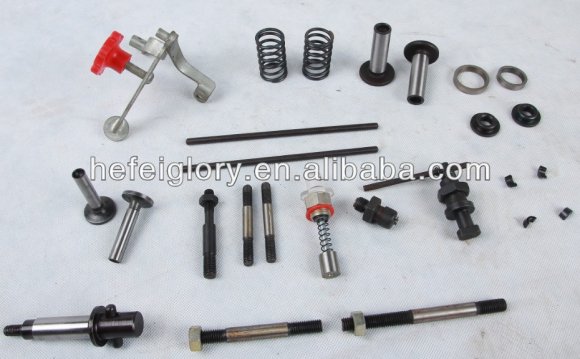
FAS | Military | DOD 101 | Systems | Ships | Propulsion ||||
Index | Search |
The diesel engine has become an integral part of the Navy's propulsion capabilities. It involves the combustion of a suitable fuel inside a cylinder containing a piston, whose motion results from the transformation of thermal energy into mechanical work. Today, diesel engines are used extensively in the Navy, serving as propulsion units for small boats, ships and land vehicles. They are also used as prime movers in auxiliary machinery, such as emergency diesel generators, pumps and compressors. Over one hundred years ago, in a letter to his former tutor Carl von Linde, Rudolph Diesel wrote: "I have some exciting news; I have found an engine which, according to my calculations, consumes only approximately one tenth of the coal required by our contemporary steam engines." With great conviction, Rudolph Diesel developed the first four-stroke diesel engine from his initial mathematical calculations. Its high efficiency placed everything that had gone before it in the shade. With equal conviction, we have optimized his invention with direct injection and turbocharging. The objectives may have changed somewhat, but the conviction with which Rudolph Diesel worked on his engine is now a major means of ship propulsion and electrical power generation. The world's very first diesel engine was developed to maturity in Augsburg, Germany between 1893 and 1897, in collaboration with its famous inventor. The following milestones have played a major pioneering role in the development of today's diesel engine: Between 1901 and 1934 the first four stroke trunk type piston engine was developed, a large diesel engine power plant was established in Kiev, the motor ship Selandia was outfitted with the first marine diesel engine and the first four stroke turbo charged diesel was developed.
In 1935 the first heavy-oil burning four-stroke diesel was manufactured. In 1952 the two-stroke diesel was introduced and in 1987 MAN B&W. The Queen Elizabeth 2 had nine such engines generating a combined output of 132, 000 bhp, giving her the most output of her time.
Two of the more common small boat engines used in the Navy today are the 6-71 General Motors Detroit Diesel engine and the Westerbeke Model 4-107. The reason for their popularity is that they are reliable and parts are easy to obtain.
Medium-sized combatant ships and many auxiliary vessels are powered by large (~50, 000 Bhp ) single-unit diesel engines or, for more economy and operational flexibility, by combinations of somewhat smaller engines. Diesel engines have relatively high efficiency at partial load, and much higher efficiency at very low partial load than steam turbines. They also have greater efficiency at high speeds than any of the other fossil-fueled plants. Thus they require the least weight of fuel for a given endurance. Other advantages include low initial cost and relatively low RPM, the latter resulting in small reduction gears. Additionally, diesel engines can be brought on-line from cold conditions rapidly. They are reliable and simple to operate and maintain, having a long history of active development for marine use.Large diesel plants have been adapted for use in the Navy on the LSD-41 (Whidbey Island) class (two medium-speed diesel engines drive each of the two shafts). In general, however, the use of diesels on intermediate sized combatants and larger requires that several smaller units be combined to drive a common shaft. This requirement results in severe space and arrangement problems. Among other disadvantages is the fact that periodic engine overhaul and progressive maintenance are required. These result in frequent down periods, which, because of the number of similar units, may not increase the amount of necessary in-port maintenance time, but do decrease the amount of time the ship has full power available while at sea. Finally, the marine diesel has a high rate of lube oil consumption, which may approach 5% of the fuel consumption; thus large quantities of lube oil must be carried.
The moving parts of the diesel engine provide for controlling the elements necessary for combustion and the transformation of combustion to mechanical shaft energy. The major moving components are the crankshaft, piston assembly, connecting rod, camshaft, valves, operating gear, flywheel, vibration dampener and various gears.For a diesel engine to start, it must turn over fast enough to obtain sufficient heat to ignite the fuel-air mixture. Combustion forces the piston down or outward (power stroke) from rapid expansion of the gases. Some factors that effect the starting of an engine include: ambient temperature, compression in the cylinders from excessive wear (low) or newly overhauled engine (high), load on the engine (attached generator) and proper pre-lubrication of the engine bearings prior to starting.
There are two extremes of diesel engine maintenance and overhaul philosophy: run the engine until it breaks and then repair it (usually at the most inopportune time) or continuously tear it down to inspect and replace worn parts. Neither of these philosophies is cost effective nor do they increase engine availability. Monitoring the operational parameters of a diesel engine by plotting and analyzing their values is a proven way to disclose the mechanical condition of a diesel engine. As engine components wear, the operating parameters gradually change with time. Diesel engine trend analysis is the collection and analysis of diesel engine operating parameters for the purpose of predicting the need for corrective maintenance/overhaul. This data can be analyzed to determine the condition of the engine's internal components and critical support systems. Trend analysis and condition based maintenance are logical methods of determining the need for major engine maintenance actions and has been in use in Navy applications since the late 1960's.RELATED VIDEO
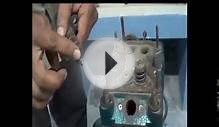
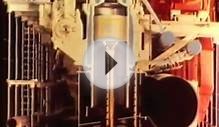
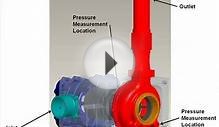