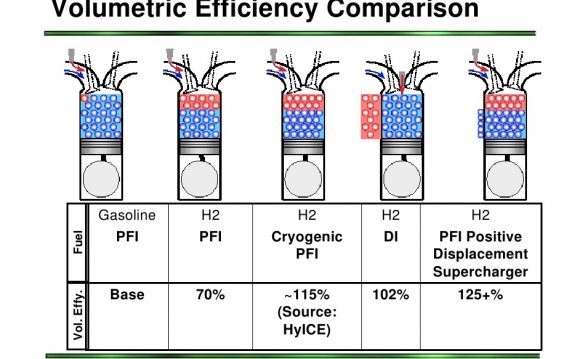
The volume of air -fuel mixture drawn into the cylinder at atmospheric pressure during the intake strokes compared to the volume of the cylinder, is known as volumetric efficiency
Internal combustion engines[edit]
Volumetric efficiency in the internal combustion engine design refers to the efficiency with which the engine can move the charge into and out of the cylinders. More specifically, volumetric efficiency is a ratio (or percentage) of the quantity of air that is trapped by the cylinder during induction over the swept volume of the cylinder under static conditions. Volumetric Efficiency can be improved in a number of ways, most effectively this can be achieved by compressing the induction charge (forced induction) or by aggressive cam phasing in naturally aspirated engines as seen in racing applications. In the case of forced induction volumetric efficiency can exceed 100%.
There are several ways to improve volumetric efficiency, but a system wide approach must be used to fully realize potential.
Many high performance cars use carefully arranged air intakes and tuned exhaust systems that use pressure waves to push air into and out of the cylinders, making use of the resonance of the system. Two-stroke engines are very sensitive to this concept and can use expansion chambers that return the escaping air-fuel mixture back to the cylinder. A more modern technique for 4 stroke engines, variable valve timing, attempts to address changes in volumetric efficiency with changes in speed of the engine: at higher speeds the engine needs the valves open for a greater percentage of the cycle time to move the charge in and out of the engine.
Volumetric efficiencies above 100% can be reached by using forced induction such as supercharging or turbocharging. With proper tuning, volumetric efficiencies above 100% can also be reached by naturally aspirated engines. The limit for naturally aspirated engines is about 100%; these engines are typically of a DOHC layout with four valves per cylinder. This process is called Inertial Supercharging and uses the resonance of the intake manifold and the mass of the air to achieve pressures greater than atmospheric at the intake valve. With proper tuning (and dependent on the need for sound level control), VE's of up to 130% have been reported in various experimental studies.
More "radical" solutions include the sleeve valve design, in which the valves are replaced outright with a rotating sleeve around the piston, or alternately a rotating sleeve under the cylinder head. In this system the ports can be as large as necessary, up to that of the entire cylinder wall. However, there is a practical upper limit due to the strength of the sleeve, at larger sizes the pressure inside the cylinder can "pop" the sleeve if the port is too large.
RELATED VIDEO
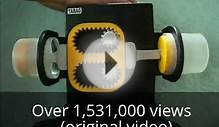
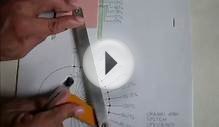
