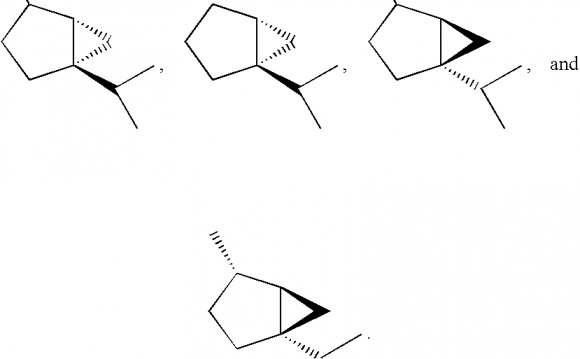
A prime mover in which the fuel is burned within the engine and the products of combustion serve as the thermodynamic fluid, as with gasoline and diesel engines.
A prime mover, the fuel for which is burned within the engine, as contrasted to a steam engine, for example, in which fuel is burned in a separate furnace. See Engine
The most numerous of internal combustion engines are the gasoline piston engines used in passenger automobiles, outboard engines for motor boats, small units for lawn mowers, and other such equipment, as well as diesel engines used in trucks, tractors, earth-moving, and similar equipment. For other types of internal combustion engines See Gas turbine, Rocket propulsion, Rotary engine, Turbine propulsion
The aircraft piston engine is fundamentally the same as that used in automobiles but is engineered for light weight and is usually air cooled. See Reciprocating aircraft engine
Characteristic features common to all commercially successful internal combustion engines include (1) the compression of air, (2) the raising of air temperature by the combustion of fuel in this air at its elevated pressure, (3) the extraction of work from the heated air by expansion to the initial pressure, and (4) exhaust. In 1862 Beau de Rochas proposed the four-stroke engine cycle as a means of accomplishing these conditions in a piston engine (see illustration). The engine requires two revolutions of the crankshaft to complete one combustion cycle. The first engine to use this cycle successfully was built in 1876 by N. A. Otto. See Otto cycle
Two years later Sir Dougald Clerk developed the two-stroke engine cycle by which a similar combustion cycle required only one revolution of the crankshaft. In 1891 Joseph Day simplified the two-stroke engine cycle by using the crankcase to pump the required air. Engines using this two-stroke cycle today have been further simplified by use of a third cylinder port which dispenses with the crankcase check valve used by Day. Such engines are in wide use for small units where fuel economy is not as important as mechanical simplicity and light weight. They do not need mechanically operated valves and develop one combustion cycle per crankshaft revolution. Nevertheless they do not develop twice the power of four-stroke cycle engines with the same size working cylinders at the same number of revolutions per minute (rpm). The principal reasons for this are (1) the reduction in effective cylinder volume due to the piston movement required to cover the exhaust ports, (2) the appreciable mixing of burned (exhaust) gases with the combustible mixture, and (3) the loss of some combustible mixture with the exhaust gases.
About 20 years after Otto first ran his engine, Rudolf Diesel successfully demonstrated an entirely different method of igniting fuel. Air is compressed to a pressure high enough for the adiabatic temperature to reach or exceed the ignition temperature of the fuel. Because this temperature is 1000°F (538°C) or higher, compression ratios of 12:1 to 23:1 are used commercially with compression pressures from about 440 to 800 psi (3 to 5.5 megapascals). The fuel is injected into the cylinders shortly before the end of the compression stroke, at a time and rate suitable to control the rate of combustion. See Diesel engine, Fuel injection
There are many characteristics of the diesel engine which are in direct contrast to those of the Otto engine. The higher the compression ratio of a diesel engine, the less the difficulties with ignition time lag. Too great an ignition lag results in a sudden and undesired pressure rise which causes an audible knock. In contrast to an Otto engine, knock in a diesel engine can be reduced by use of a fuel of higher cetane number, which is equivalent to a lower octane number.
The larger the cylinder diameter of a diesel engine, the simpler the development of good combustion. In contrast, the smaller the cylinder diameter of the Otto engine, the less the limitation from detonation of the fuel.
High intake-air temperature and density materially aid combustion in a diesel engine, especially of fuels having low volatility and high viscosity. Some engines have not performed properly on heavy fuel until provided with a supercharger. The added compression of the supercharger raised the temperature and, what is more important, the density of the combustion air. For an Otto engine, an increase in either the air temperature or density increases the tendency of the engine to knock and therefore reduces the allowable compression ratio.
Diesel engines develop increasingly higher indicated thermal efficiency at reduced loads because of leaner fuel-air ratios and earlier cutoff. Such mixture ratios may be leaner than will ignite in an Otto engine. Furthermore, the reduction of load in an Otto engine requires throttling, which develops increasing pumping losses in the intake system.