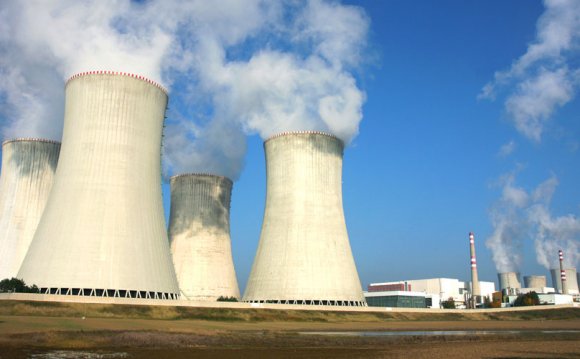
A heat recovery loop design method with variable temperature storage is proposed.
Constant and variable temperature storage HRL design methods are compared.
•Integration of industrial solar into a heat recovery loop is investigated.
•Proposed integration methods are applied to a large scale dairy case study.
Solar is a renewable energy that can be used to provide process heat to industrial sites but require thermal storage. HRLs (heat recovery loops) are an indirect method for transferring heat from one process to another using an intermediate fluid. With HRL's thermal storage is also necessary to effectively meet the stop/start time dependent nature of the multiple source and sink streams. Combining solar heating with HRL's is a cost effective way to share common storage and piping infrastructure. The conventional HRL design method based on a CTS (constant temperature storage) and a new HRL design method using VTS (variable temperature storage) are applied to demonstrate the potential benefits of inter-plant heat integration and installing solar heating. The dairy case study had available 12 source streams including four spray dryer exhausts and six sink streams. The addition of the dryer exhausts as heat sources was a critical factor in gaining a heat recovery of 10.8 MW for the variable temperature storage design, of which 5.1 MW was contributed from exhaust heat recovery. For the same minimum approach temperature the VTS approach achieved 37% more heat recovery compared to the CTS approach. Solar heating also proved to be a valuable source to be integrated into an HRL with a pinch around the cold storage tank with the maximum addition of 0.9 MW of heating on average for the CTS approach and 1.0 MW of heating on average for the VTS approach.
Keywords
- Heat recovery loop;
- Low temperature heat recovery;
- Solar heating;
- Process integration