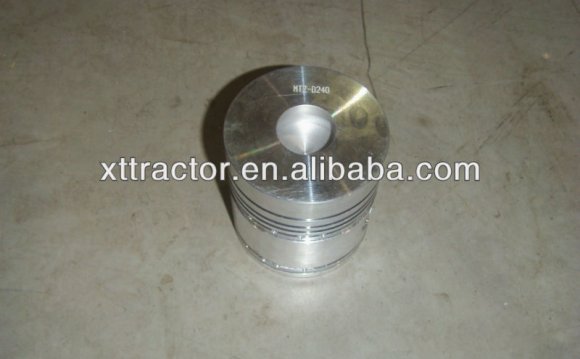
•
Six methods are used to identify piston slap events in internal combustion engines.
•The number of slap events increases as the engine speed increases.
•Quasi-static/transient force methods can predict slap position at lower engine speed.
•The transient minimum film thickness method is more successful at higher engine speed.
•The piston-impact angular duration method predicts slap events through all tests.
Piston slap is a major source of vibration and noise in internal combustion engines. Therefore, better understanding of the conditions favouring piston slap can be beneficial for the reduction of engine Noise, Vibration and Harshness (NVH). Past research has attempted to determine the exact position of piston slap events during the engine cycle and correlate them to the engine block vibration response. Validated numerical/analytical models of the piston assembly can be very useful towards this aim, since extracting the relevant information from experimental measurements can be a tedious and complicated process.
In the present work, a coupled simulation of piston dynamics and engine tribology (tribodynamics) has been performed using quasi-static and transient numerical codes. Thus, the inertia and reaction forces developed in the piston are calculated. The occurrence of piston slap events in the engine cycle is monitored by introducing six alternative concepts: (i) the quasi-static lateral force, (ii) the transient lateral force, (iii) the minimum film thickness occurrence, (iv) the maximum energy transfer, (v) the lubricant squeeze velocity and (vi) the piston-impact angular duration.
The validation of the proposed methods is achieved using experimental measurements taken from a single cylinder petrol engine in laboratory conditions. The surface acceleration of the engine block is measured at the thrust- and anti-thrust side locations. The correlation between the theoretically predicted events and the measured acceleration signals has been satisfactory in determining piston slap incidents, using the aforementioned concepts. The results also exhibit good repeatability throughout the set of measurements obtained in terms of the number of events occurring and their locations during the engine cycle.
Keywords
- Piston slap;
- Internal combustion engines;
- Tribology;
- Dynamics
1. Introduction
The ever increasing importance of fuel efficiency, noise reduction and engine performance is forcing researchers to better understand the mechanism and effective parameters of piston dynamics. The piston assembly plays a key role in the generation of engine mechanical losses, including noise . The latter is well known as piston impact (also slap) noise. In order to better study the occurrence of slap noise events, one should carefully monitor the piston׳s secondary motion, which leads to skirt-to-cylinder liner contacts. The excitation conditions (forces and moments) on the piston are responsible for the secondary motion, which occurs laterally within the clearance (translation) and around the piston pin (rotation). The schematic of these motions is given in . and ϕϕ are the crank and connecting rod angles, respectively . RR is the piston crown radius (later used to calculate the crown area). When the crankshaft rotation is clockwise, the left side of the cylinder liner is called the thrust side (TS) and the opposite side is known as the anti-thrust side (ATS). Piston impacts can occur on either side of the liner. Piston slap excites the engine block and manifests itself in the form of surface vibrations, which are eventually radiated as noise in the vicinity of the engine. In addition to the perceived benefits for engine NVH, good understanding of the number and location of piston slap events can be helpful for fuel efficiency purposes through improved system tribodynamics .
RELATED VIDEO
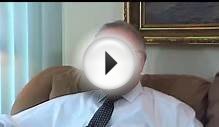
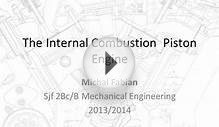