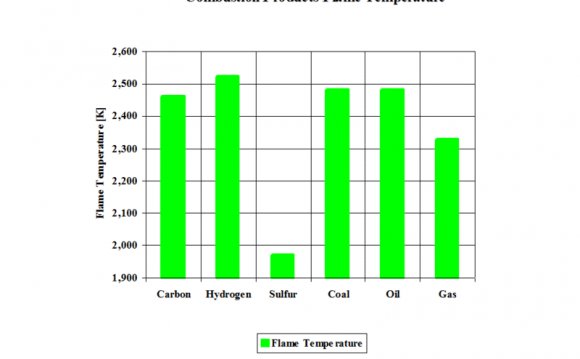
Overview[edit]
Heat engines generate mechanical power by extracting energy from heat flows, much as a water wheel extracts mechanical power from a flow of mass falling through a distance. Engines are inefficient, so more heat energy enters the engine than comes out as mechanical power; the difference is waste heat which must be removed. Internal combustion engines remove waste heat through cool intake air, hot exhaust gases, and explicit engine cooling.
Engines with higher efficiency have more energy leave as mechanical motion and less as waste heat. Some waste heat is essential: it guides heat through the engine, much as a water wheel works only if there is some exit velocity (energy) in the waste water to carry it away and make room for more water. Thus, all heat engines need cooling to operate.
Cooling is also needed because high temperatures damage engine materials and lubricants. Cooling becomes more important in when the climate becomes very hot. Internal-combustion engines burn fuel hotter than the melting temperature of engine materials, and hot enough to set fire to lubricants. Engine cooling removes energy fast enough to keep temperatures low so the engine can survive.
Some high-efficiency engines run without explicit cooling and with only incidental heat loss, a design called adiabatic. Such engines can achieve high efficiency but compromise power output, duty cycle, engine weight, durability, and emissions.
Basic principles[edit]
Most internal combustion engines are fluid cooled using either air (a gaseous fluid) or a liquid coolant run through a heat exchanger (radiator) cooled by air. Marine engines and some stationary engines have ready access to a large volume of water at a suitable temperature. The water may be used directly to cool the engine, but often has sediment, which can clog coolant passages, or chemicals, such as salt, that can chemically damage the engine. Thus, engine coolant may be run through a heat exchanger that is cooled by the body of water.
Most liquid-cooled engines use a mixture of water and chemicals such as antifreeze and rust inhibitors. The industry term for the antifreeze mixture is engine coolant. Some antifreezes use no water at all, instead using a liquid with different properties, such as propylene glycol or a combination of propylene glycol and ethylene glycol. Most "air-cooled" engines use some liquid oil cooling, to maintain acceptable temperatures for both critical engine parts and the oil itself. Most "liquid-cooled" engines use some air cooling, with the intake stroke of air cooling the combustion chamber. An exception is Wankel engines, where some parts of the combustion chamber are never cooled by intake, requiring extra effort for successful operation.
There are many demands on a cooling system. One key requirement is to adequately serve the entire engine, as the whole engine fails if just one part overheats. Therefore, it is vital that the cooling system keep all parts at suitably low temperatures. Liquid-cooled engines are able to vary the size of their passageways through the engine block so that coolant flow may be tailored to the needs of each area. Locations with either high peak temperatures (narrow islands around the combustion chamber) or high heat flow (around exhaust ports) may require generous cooling. This reduces the occurrence of hot spots, which are more difficult to avoid with air cooling. Air-cooled engines may also vary their cooling capacity by using more closely spaced cooling fins in that area, but this can make their manufacture difficult and expensive.
Only the fixed parts of the engine, such as the block and head, are cooled directly by the main coolant system. Moving parts such as the pistons, and to a lesser extent the crank and rods, must rely on the lubrication oil as a coolant, or to a very limited amount of conduction into the block and thence the main coolant. High performance engines frequently have additional oil, beyond the amount needed for lubrication, sprayed upwards onto the bottom of the piston just for extra cooling. Air-cooled motorcycles often rely heavily on oil-cooling in addition to air-cooling of the cylinder barrels.
Liquid-cooled engines usually have a circulation pump. The first engines relied on thermo-syphon cooling alone, where hot coolant left the top of the engine block and passed to the radiator, where it was cooled before returning to the bottom of the engine. Circulation was powered by convection alone.
Other demands include cost, weight, reliability, and durability of the cooling system itself.
Conductive heat transfer is proportional to the temperature difference between materials. If engine metal is at 250 °C and the air is at 20°C, then there is a 230°C temperature difference for cooling. An air-cooled engine uses all of this difference. In contrast, a liquid-cooled engine might dump heat from the engine to a liquid, heating the liquid to 135°C (Water's standard boiling point of 100°C can be exceeded as the cooling system is both pressurised, and uses a mixture with antifreeze) which is then cooled with 20°C air. In each step, the liquid-cooled engine has half the temperature difference and so at first appears to need twice the cooling area.
However, properties of the coolant (water, oil, or air) also affect cooling. As example, comparing water and oil as coolants, one gram of oil can absorb about 55% of the heat for the same rise in temperature (called the specific heat capacity). Oil has about 90% the density of water, so a given volume of oil can absorb only about 50% of the energy of the same volume of water. The thermal conductivity of water is about 4 times that of oil, which can aid heat transfer. The viscosity of oil can be ten times greater than water, increasing the energy required to pump oil for cooling, and reducing the net power output of the engine.
RELATED VIDEO
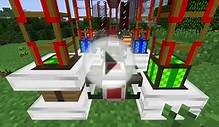
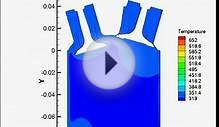
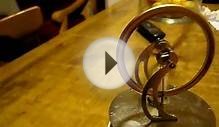